14
2024-11
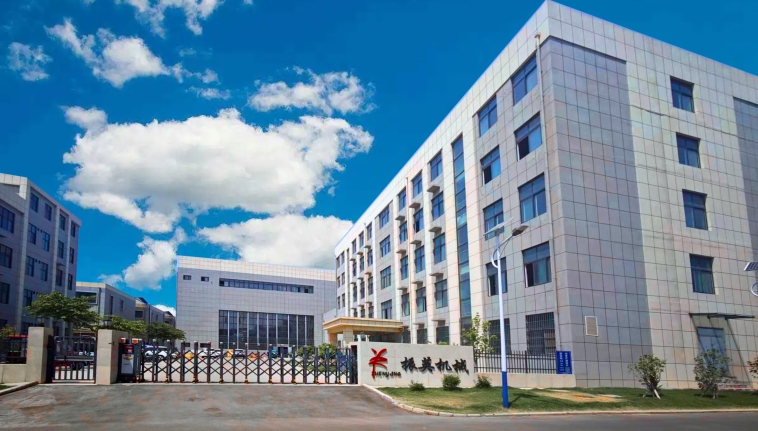
Xinxiang Zhenying Machinery Equipment Co., Ltd. has obtained a patent for the assembly tooling of rotary vibrating screen screening components, solving the problem of time-consuming and laborious asse
According to the information of the China National Intellectual Property
Administration, Xinxiang Zhenying Mechanical Equipment Co., Ltd. has obtained a
patent entitled "a kind of assembly tooling for the screening component of the
rotary vibrating screen", with the authorization announcement number of CN
221967899 U and the application date of December 2023. The patent abstract shows that this utility model discloses an assembly
fixture for a rotary vibrating screen screening component, which relates to the
field of mechanical processing technology. The utility model comprises a support
base and an elastic positioning plate. The inner edge of the support base is
clamped with multiple lifting cylinders, and the top of each lifting cylinder is
provided with a support plate. One side of each support plate is provided with
an elastic positioning plate, and one side of each elastic positioning plate is
provided with a positioning cylinder. The top of each elastic positioning plate
is fitted with a rotating roller. This utility model solves the problem of
time-consuming and laborious assembly between multiple outer frames during the
assembly process of the rotary vibrating screen screening component assembly
fixture by setting up a support base and an elastic positioning plate, and the
relatively large size of the outer frames requires repeated rotation and
handling of multiple outer frames during assembly.
MORE
11
2024-11
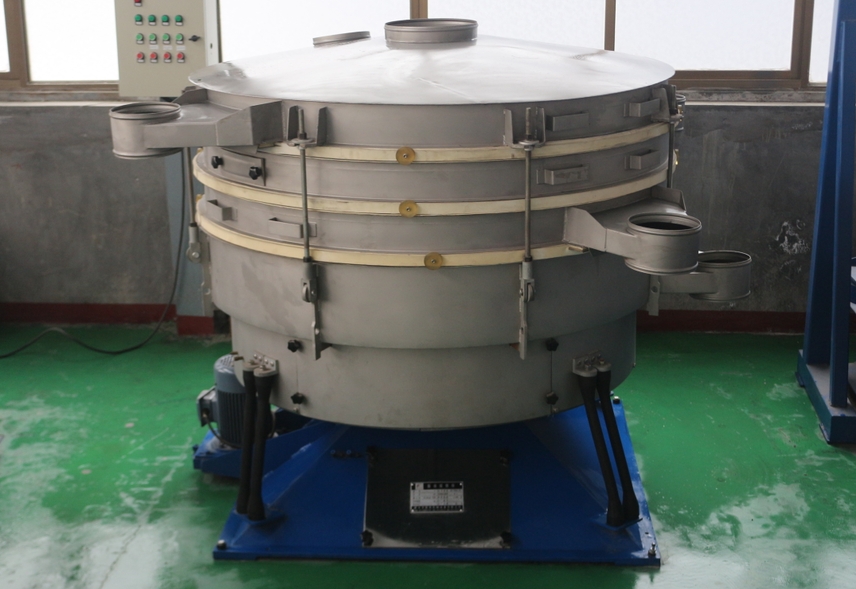
What are the requirements for installing a swing screen?
Reasonable installation of swing screens can effectively extend the service
life and production efficiency of equipment. So what are the issues to pay
attention to when installing the swing screen? Swing screen manufacturers now
take you to understand: When installing the motor, it should be installed horizontally, and the
surface should be kept flat and smooth. After the motor is installed, its
firmness and reliability should be ensured, and the installation surface should
also be kept smooth and flat, so as to ensure that people can use it more
conveniently and simply. When installing the swing screen, it is necessary to follow the
installation drawings, and the supporting frame needs to be installed
horizontally on the foundation, which should also have sufficient rigidity and
strength to better support the entire load of the swing screen. After installing the equipment, check whether the transportation support
has been removed. The transportation support plays a role in protecting the
screening machine during transportation. If it is not removed, the equipment
will not operate normally, thereby affecting its service life. The manufacturer of the swing screen reminds that maintenance work after
installation is indispensable. After installing the swing screen, it is
necessary to check whether each component of the equipment is normal. Check if
the screen mesh is damaged, and if found, immediately contact the supplier. Install the electric motor and triangular tape. When installing, the
foundation of the motor should be leveled, the level of the motor needs to be
calibrated, the center lines of the grooves corresponding to the two tape wheels
should coincide, and the tension of the triangular tape should be
appropriate. Check the fixing condition of each connecting component of the sieve (such
as sieve plate, exciter, etc.). The sieve should be evenly tensioned to prevent
local vibration. Check the lubrication condition of the transmission part,
whether the wiring of the motor and control box is correct, and manually rotate
the transmission part to check if it is running normally.
MORE
07
2024-11

How to solve the problem of slow discharge of linear vibrating screen?
1. Check whether the screen mesh and the discharge port are level or too
high. Generally, they should be about 5mm higher, and the height of the
discharge port should be designed differently according to the characteristics
of different materials. 2. When the linear vibrating screen or ultrasonic vibrating screen is
working, check whether the screen surface or discharge port is in a horizontal
state, which directly affects the screening effect of the equipment; If it is
not horizontal, it should be adjusted in a timely manner. The vibrating screen
is equipped with supporting feet, and customers can adjust the feet to make the
vibrating screen meet the horizontal requirements and lower it
appropriately. 3. In addition to the above situations, the key point is that the angle of
the upper and lower eccentric blocks of the vibration motor can be adjusted. A
smaller angle allows the material to spread outwards faster, while a larger
angle slows down the outward spread of the material. When changing the angle of
the eccentric block of the vibration motor, it should be adjusted by about 5
degrees. If you have strict requirements for screening accuracy, the angle of
the motor should not be too small, otherwise the material will quickly scatter
outward, which is not conducive to the screening effect. Generally, the
eccentric block angle of the vibration screen is 45 degrees when it leaves the
factory.
MORE
06
2024-11
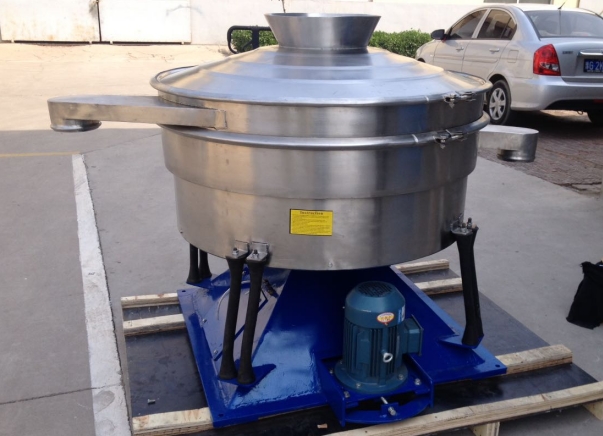
What are the characteristics of a circular swing screen?
What are the characteristics of a circular swing screen? Circular swing
screens are mainly used for screening fine and ultrafine powders, and are
particularly suitable for materials that are difficult to process. They are also
the most commonly used type of vibrating screen. Zhenying Machinery is a
professional manufacturer of swing screens, and circular swing screens generally
have the following characteristics: 1. Mainly used for soft rock screening, it will not damage the original
structure of the wool particles and is not prone to static electricity. It is
very suitable for screening materials that are flammable, explosive, and prone
to static electricity, and can effectively extend the service life of equipment
components. 2. The circular swing screen imitates the manual screening action and
process. The material moves in a gradually opening spiral motion on the screen
surface, allowing the material to travel a long distance in relative area, and
the screening accuracy can reach 90-95%. 3. Adopting a circular building block assembly structure, assembly and
disassembly are simpler, and the discharge port can rotate 360 degrees
freely. 4. The vertical acceleration value of material particles during the
screening process is low, so the screen mesh is not easily damaged and can
effectively extend its service life. 5. The circular swing screen has advanced anti clogging technology and five
different cleaning methods, which can make the screen holes less prone to
clogging and ensure the continuity of screening.
MORE
05
2024-11
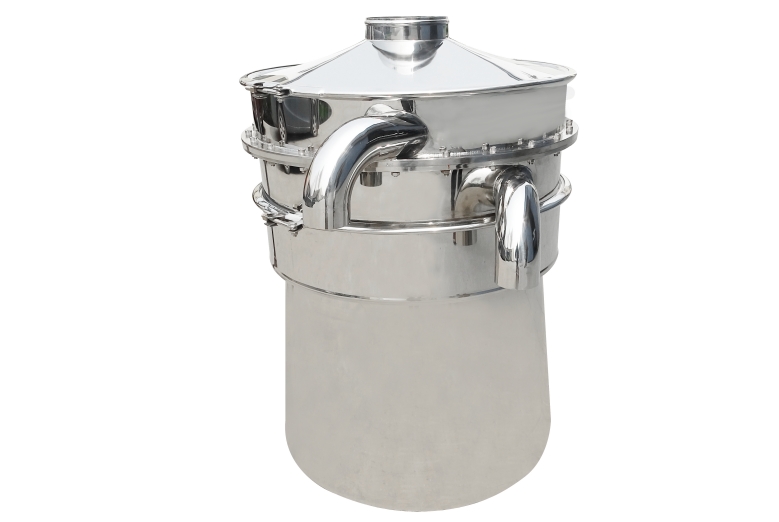
How to maintain and upkeep chemical vibrating screens?
Chemical vibrating screen is a general term for vibrating screens used in
the chemical industry for screening operations. It is a commonly used machine
equipment in the chemical industry. Due to its contact with chemical raw
materials, chemical vibrating screens require daily maintenance and upkeep to
better extend their service life. The maintenance and upkeep of chemical
vibrating screens should pay attention to the following aspects: Firstly, the spring components of the chemical vibrating screen need to be
checked for looseness. If there is looseness, it needs to be tightened with a
wrench to achieve an ideal screening effect. Secondly, the chemical vibrating screen should also be regularly inspected
for any damage to the surface of the screen mesh. If any damage is found, it
should be replaced in a timely manner to avoid poor screening of the
product. Thirdly, we also need to regularly inspect the motor of the chemical
vibrating screen and add butter from the grease nozzle. Finally, it is also important to pay attention to whether the V-shaped ring
of the screening frame of the chemical vibrating screen is damaged. If it is
damaged, it should be repaired in a timely manner to avoid material leakage.
MORE
05
2024-11

What factors determine the price of vibrating screens?
We all know that there are many vibrating screen factories on the market at
present, and the prices are also different. So, what factors cause the
differences in vibrating screen prices? Firstly, the material of the vibrating screen: The vibrating screen is
generally made of Q235 carbon steel and 304 stainless steel, but these two types
of materials also have advantages and disadvantages, mainly due to the thickness
of the plate. The thickness of the plate used by regular vibrating screen
manufacturers is basically 2.0mm, so we need to pay attention when
purchasing. Secondly, production design: Regardless of the type of vibrating screen
equipment, design and manufacturing processes are important. Only by designing a
reasonable product can we save costs for users and improve the overall quality
of the product. In addition, there are related accessories: the core components of the
vibrating screen include a cleaning device, dust prevention device, vibration
spring, vibration motor, etc. The quality of accessories is related to the
accuracy and service life of screening! Therefore, when purchasing vibrating
screens, we should pay extra attention to whether they are accessories produced
by legitimate manufacturers. Finally, there is after-sales service: vibration screen factories with
comprehensive after-sales service generally have higher costs than those without
after-sales service, which to some extent also affects the price of vibration
screens. The above are the main factors that affect the price of vibrating
screens.
MORE
02
2024-11

How does the vibrating screen factory teach you to check the vibrating screen?
We all know that a vibrating screen is a screening machinery that requires
frequent continuous operation. Therefore, in order to ensure the normal
operation of the equipment and a longer service life, daily inspection and
troubleshooting are necessary. Next, we will teach you how to inspect a
vibrating screen. 1. Firstly, the vibrating screen should be promptly cleaned internally
after each use. 2. Carefully check whether the fastening bolts at each joint of the
vibrating screen are loose. If there is any looseness, it needs to be tightened
or replaced in a timely manner to avoid further operation. Vibrating screen factory 3. Check if the wiring from the vibration motor to the switch is worn. If
severe damage is found, replacement is also necessary. 4. In addition, it is necessary to check whether the mesh is tensioned and
whether the mesh surface is damaged. If there is any damage, the mesh should be
replaced in a timely manner. 5. Then check if there are any abnormal sounds or heating conditions in the
motor. If it is abnormal, add lubricating oil or replace the bearings. In
addition, the maintenance of the vibrating screen motor should be done by
skilled technicians with professional knowledge.
MORE
31
2024-10
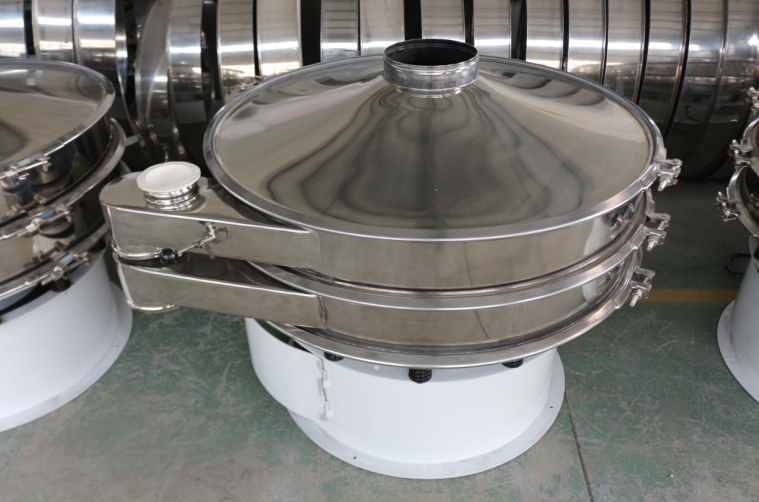
Advantages and application scenarios of chili powder vibrating screen
Chili powder vibrating screen is a specialized equipment used for screening
and grading chili powder. It usually uses vibration screening technology, where
the vibration force generated by the vibrator is transmitted to the screening
body, allowing the chili powder to be screened on the screen. This device can
effectively remove impurities and particles from chili powder, achieving precise
particle separation and screening. Chili powder vibrating screen usually has the
advantages of high speed, precision, and energy saving, which helps to improve
the quality and market competitiveness of chili powder. It plays an important
role in the production and processing of chili powder, helping manufacturers
improve production efficiency and product quality. Advantages of chili powder vibrating screen: 1. High speed screening: The chili powder vibrating screen adopts the
action of vibration force and screen mesh, which has a large screening area and
high screening efficiency. It can process a large amount of chili powder and
complete the screening process in a short time, improving production
efficiency. 2. Precise grading: The chili powder vibrating screen is equipped with
screens of different aperture sizes to achieve grading of chili powder, ensuring
product consistency and quality. 3. Removing impurities: The chili powder vibrating screen can remove
impurities and non compliant particles from the chili powder through the action
of a sieve, improving the purity and quality of the chili powder. 4. Maintain raw material characteristics: The chili powder vibrating screen
adopts non-contact screening during the screening process, which will not cause
damage or breakage to the chili powder, and can maintain the original shape and
characteristics of the chili powder. 5. Adjustable: The vibration force and mesh aperture of the chili powder
vibrating screen can be adjusted as needed. According to different processing
requirements of chili powder, the intensity and frequency of vibration force can
be adjusted, and different mesh sizes can be used to achieve the desired
screening effect. Application scenarios: 1. Chili powder production: The chili powder vibrating screen is one of the
important equipment on the chili powder production line. It can screen, grade,
and remove impurities from chili powder to ensure its quality and purity. 2. Chili powder processing: Chili powder vibrating screen can be used in
the processing of chili products. It can screen and remove impurities from chili
powder to ensure product quality and purity during the processing. 3. Chili planting: In the field of chili planting, chili powder vibrating
screens can be used to screen and grade chili seeds. By screening and removing
seeds that do not meet the requirements, the quality and germination rate of
seeds can be improved, providing good germplasm resources for pepper
cultivation. 4. Chili powder trade: Chili powder vibrating screens play an important
role in chili powder trade. In the export and process of chili powder, it is
necessary to screen and grade the products to meet the quality standards and
requirements of different countries and regions in China, ensuring that the
products meet trade standards.
MORE
31
2024-10

Advantages and application scenarios of ceramic glaze vibrating screen
Ceramic glaze vibrating screen is a specialized equipment used for
screening and grading ceramic glazes. It plays an important role in the ceramic
industry, controlling the particle size and distribution of glazes to improve
the quality and appearance of ceramic products. The design of ceramic glaze
vibrating screen considers the characteristics of ceramic glaze, such as
particle size, shape and density, to ensure the screening effect and production
efficiency. Advantages of ceramic glaze vibrating screen: 1. Fine screening effect: Ceramic glaze vibrating screen can achieve
particle size distribution and separation of glaze particles by adjusting the
sieve aperture and vibration parameters, ensuring the uniformity and consistency
of glaze and improving the quality of ceramic products. 2. Extremely high production capacity: The ceramic glaze vibrating screen
has screening ability, which can quickly process a large number of glaze
particles, reducing production time and labor costs. 3. Removing impurities and unqualified particles: Ceramic glaze vibrating
screens can effectively remove impurities and unqualified glaze particles.
Through the screening process, it can separate out particles that are too large
or too small as well as other impurities, ensuring the purity and quality of the
glaze. 4. Customizable and adaptable: Ceramic glaze vibrating screens can be
customized according to different processes and product requirements. Users can
choose the appropriate mesh aperture and vibration parameters to meet their
specific screening goals and standards. 5. Save resources and costs: By using ceramic glaze vibrating screens, the
waste and loss of glaze can be reduced. It can separate qualified glaze
particles, avoid unnecessary resource waste, and reduce production costs. Application scenarios of ceramic glaze vibrating screen: 1. Ceramic glaze production: In the production process of ceramic glaze,
ceramic glaze vibrating screens are used to screen impurities and particles of
different sizes in the raw materials, ensuring the quality and uniformity of the
glaze. 2. Ceramic product production: In the production process of ceramic
products, ceramic glaze vibrating screens are used to screen and grade ceramic
glazes to ensure the surface smoothness and quality consistency of the
products. 3. Ceramic decoration: In the process of ceramic decoration, ceramic glaze
vibrating screens are used to screen pigments and glazes of different particle
sizes, in order to achieve precise control of the decorative effect. 4. Ceramic technology research and development: In the stage of ceramic
technology research and development, ceramic glaze vibrating screens can be used
to screen different formulas of glazes and pigments, helping R&D personnel
optimize the process. 5. Ceramic waste treatment: In the process of ceramic waste treatment,
ceramic glaze vibrating screens can be used to screen and recycle waste ceramic
particles, achieving resource reuse and reducing waste.
MORE
31
2024-10
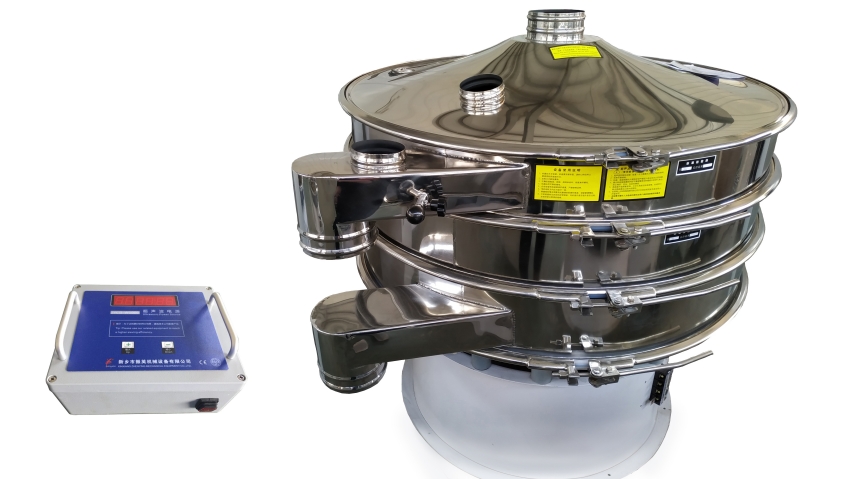
The advantages and applications of ultrasonic vibrating screen for putty powder
What screening equipment is used for putty powder? Ultrasonic vibrating
screen is a device that uses ultrasonic vibration technology to screen and grade
putty powder (also known as gypsum powder). This device combines ultrasonic
technology and traditional vibration screening technology, aiming to improve the
screening efficiency and quality of putty powder. The function of ultrasonic vibrating screen for putty powder The ultrasonic vibrating screen for putty powder plays a crucial role as a
screening equipment in the production process of putty powder. Its impurity
removal and grading functions ensure the quality and stability of putty powder
products. Removing impurities: During the production process, putty powder inevitably
contains some impurities such as stones, sawdust, fibers, etc. Ultrasonic
vibrating screen uses high-frequency vibration to make materials jump and roll
on the screen surface, thereby removing these impurities and ensuring the purity
of putty powder. Grading: Ultrasonic vibrating screens can be used to grade putty powder by
replacing screens with different mesh sizes, resulting in powders of different
particle sizes. Preventing screen clogging: Ultrasonic vibration can destroy the static
electricity and adhesion between materials, prevent screen clogging, and ensure
screening efficiency. Application scenarios of ultrasonic vibrating screen for putty powder Putty powder ultrasonic vibrating screen has a wide range of application
scenarios in building materials, chemical and other related industries, mainly
including the following aspects: Production of building materials: In the production process of gypsum
products such as gypsum boards, gypsum lines, and gypsum slabs, ultrasonic
vibrating screens for putty powder are widely used for screening and grading
putty powder to ensure product quality. In the field of architectural decoration, ultrasonic vibrating screens are
used for screening and processing putty powder in indoor decoration and coating
construction, ensuring the fineness and uniformity of putty powder and improving
the quality of coatings. Chemical industry: In chemical production, ultrasonic vibrating screens for
putty powder can be used for screening and processing catalysts to improve their
activity and stability. Food industry: In food processing, putty powder ultrasonic vibrating screen
can be used for screening food raw materials such as flour and starch to ensure
food quality. Drug production: In the pharmaceutical industry, putty powder ultrasonic
vibrating screen can be used for screening and grading drug raw material powders
to ensure the purity and uniformity of drugs. The ultrasonic vibrating screen for putty powder has multiple advantages
compared to traditional vibrating screens, mainly including the following
points: Improving screening efficiency: Ultrasonic vibration technology can improve
the screening efficiency of putty powder, accelerate the screening process,
reduce screen hole blockage, and thus improve production efficiency. Improve screening accuracy: Ultrasonic vibrating screen can separate small
particles, reduce adhesion between particles, improve screening accuracy, and
ensure product quality. Reduce energy consumption: Compared to traditional vibrating screens,
ultrasonic vibrating screens for putty powder can usually reduce energy
consumption, improve energy utilization efficiency, and save production
costs. Reduce sieve blockage: Ultrasonic vibration technology can prevent sieve
holes from being blocked by particles, keep the sieve mesh unobstructed, and
ensure a continuous and stable screening process. Extending equipment lifespan: Ultrasonic vibrating screens use
high-frequency vibration technology to reduce excessive wear on the screen mesh,
extend equipment lifespan, and reduce maintenance costs. Improving production quality: By improving screening accuracy and
efficiency, ultrasonic vibrating screens for putty powder can help manufacturers
improve product quality and meet customer needs. Strong adaptability: The design of ultrasonic vibrating screen is flexible
and diverse, and can be customized according to different production needs,
suitable for screening putty powder of various specifications and shapes.
MORE