14
2023-01
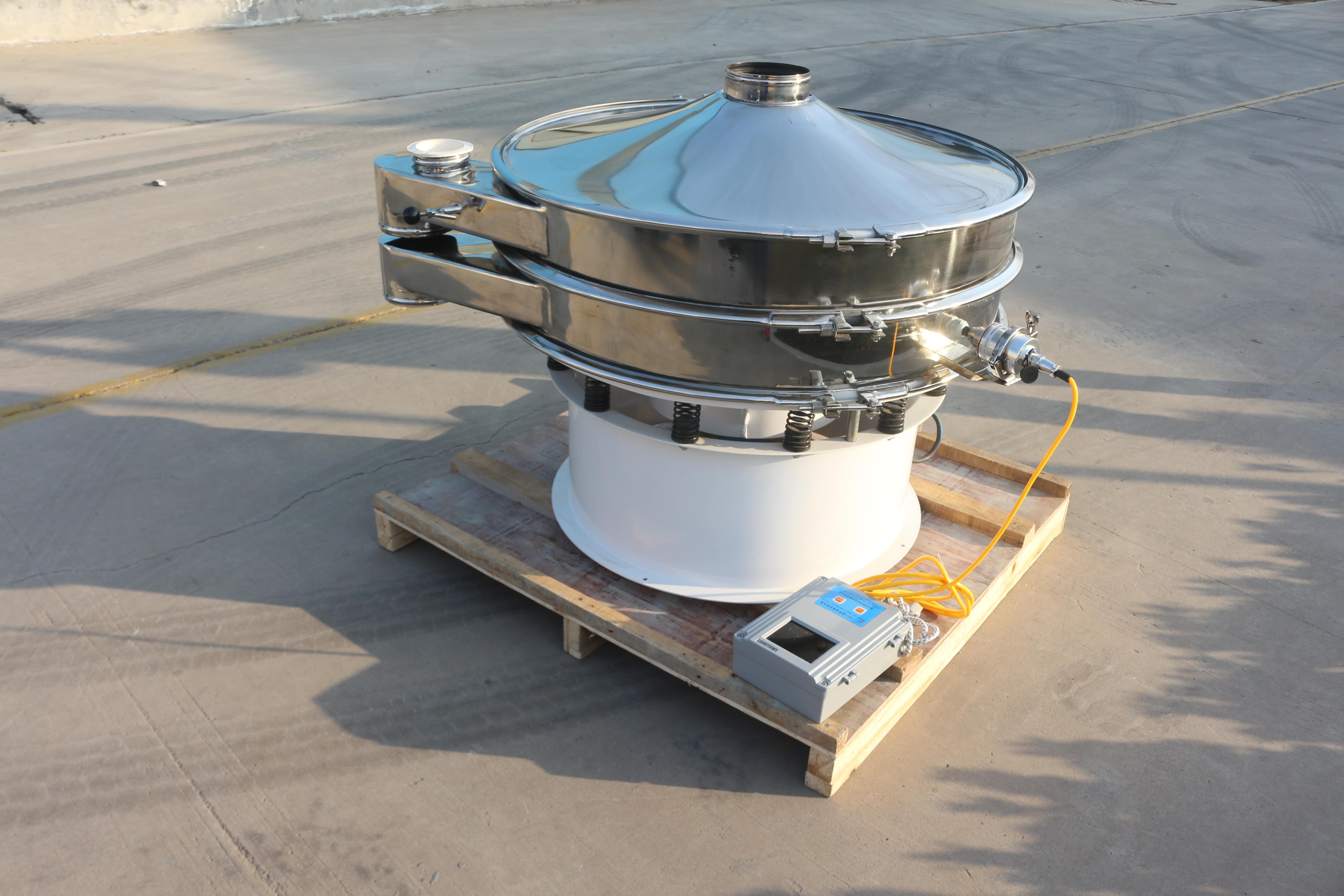
Powder sieving machine introduction
Fine Powder sieving machine Powder sieving machine usually called ultrasonic vibration sieve.In the
daily production process,many fine powder materials are screened,and these fine
powder materials are difficult to screening and the screening output small. For
this reason,Zhenying company has developed an ultra-fine powder vibrating
sieving machine(ultrasonic vibration sieve). Our fine powder sieving machine is completely independently developed,Using
self-developed ultrasonic system,The screening mesh number can reach 625 meshes,
which solves the screening problems of blockage,easy agglomeration,and high
density.Ultrasonic vibrating sieve machine adopts a special ultrasonic grid
structure.The conversion from built-in ultrasound to external ultrasound.The
external ultrasound can be replaced easily and more efficiently.highest
frequency can reach 18Hz.Compared with the ultrasonic systems of international
well-known brands,Our ultrasonic system has little difference in screening
efficiency and service life,but the price is relatively lower. Product name:Ultrasonic Vibration Sieve Screening accuracy:300-625 meshLayers:1-5 layers Powder sieving machine Advantage: 1.Accept customer customization and provide screening solutions 2.Good airtightness,environmental protection and sanitation 3.High safety and easy operation 4.The vibration frequency is adjustable,high screening accuracy,and the
screening accuracy can be increased by 30-100% Ultra-fine powder vibrating sieving machine Application: Chemical industry: washing powder, resin powder, pigment, micro powder,
paint, soda ash, lithium battery, negative electrode material, etc. Abrasive industry: quartz sand, mud, etc. Food industry: sugar, salt, alkali, monosodium glutamate, milk powder, soy
milk, yeast, fruit juice, soy sauce, vinegar, etc. Papermaking industry: coating paint, clay slurry, black and white liquid,
waste liquid, papermaking liquid, waste water recycling. Metallurgical industry: titanium oxide, zinc oxide, electromagnetic
materials, metal powder, electrode powder Powder sieving machine Precautions: 1.Each ultrasonic system includes an ultrasonic vibrating screen power
supply,an aviation connection patch cord,a transducer,and a grid.Please do not
interchange and use the ultrasonic system of other manufacturers to avoid
unnecessary loss. 2.In the case of meeting production requirements,the maximum vibration
amplitude should not exceed 200μm 3.The screen mesh must be tight,otherwise it will affect the ultrasonic
output and vibration effect 4.If the material is conductive,please use an extended ultrasonic aerial
connection cable to isolate the power supply of the ultrasonic vibrating screen
from the screening site to prevent the material from entering the power box and
causing a short circuit. 5.When replacing the screen,scrape off the residual glue on the screen with
a sharp wallpaper knife.Do not use the angle grinder wheel to polish it to
prevent damage to the Ultrasonic System.
MORE
10
2025-01
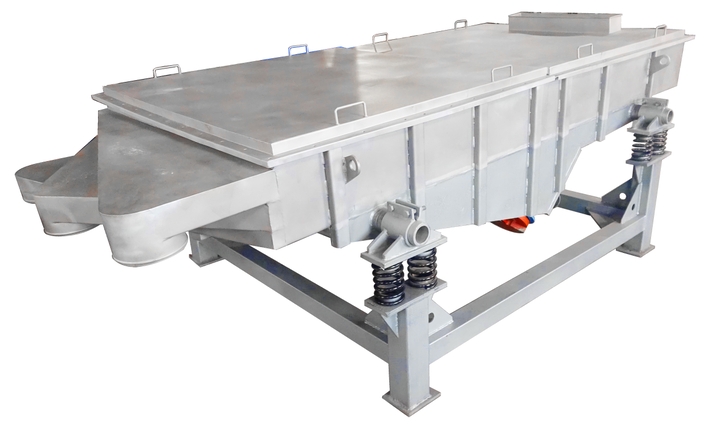
Linear Vibrating Sieve Machine: An Overview and Its Applications
Introduction The linear vibrating sieve machine is a significant piece of equipment in
the field of industrial screening and separation. It operates based on the
principle of linear vibration, which enables it to effectively classify and
separate materials according to their particle sizes or other physical
properties. With its unique design and reliable performance, it has found wide
applications in various industries. Working Principle The linear vibrating sieve machine mainly consists of a vibrating frame,
screen meshes, vibration motors, and a support structure. The vibration motors
are strategically installed on the sieve machine to generate a linear vibration
motion. When the machine is turned on, the vibration motors produce a specific
frequency and amplitude of vibration. This vibration is then transmitted to the
screen meshes, causing the materials placed on the sieve to move in a linear
direction along the surface of the screen. During this process, smaller particles are able to pass through the screen
meshes under the influence of gravity and the vibrating force, while larger
particles are retained on the screen and gradually move towards the outlet
designated for oversized materials. The adjustable vibration parameters, such as
frequency and amplitude, allow for precise control over the screening process to
meet different requirements of various materials. Advantages High Screening Efficiency: Thanks to its continuous linear vibration,
materials can be evenly distributed and screened quickly. It can handle a large
volume of materials within a relatively short time, ensuring a high throughput
rate. Accurate Separation: The ability to adjust the vibration parameters and the
selection of appropriate screen meshes make it possible to achieve highly
accurate separation of materials with different particle sizes. This is crucial
for industries where strict quality control regarding material granularity is
required. Low Noise and Energy Consumption: Compared with some other types of
screening equipment, the linear vibrating sieve machine usually operates with
relatively low noise levels. Moreover, its design and working mechanism
contribute to efficient energy utilization, reducing overall energy consumption
during operation. Versatile and Adaptable: It can be used for screening a wide variety of
materials, including powders, granules, and even small pieces of solids.
Additionally, it can be customized according to specific industrial needs, such
as adjusting the size of the sieve deck, the inclination angle, and the type of
screen mesh. Applications Food Industry In the food processing industry, the linear vibrating sieve machine plays a
vital role. For example, in the production of flour, it is used to remove
impurities like small stones, husks, and other foreign particles from the wheat
grains before milling. In the sorting of grains such as rice and corn, it can
separate out broken or underdeveloped kernels to ensure the quality of the final
food products. It is also employed in the processing of nuts, candies, and dried
fruits to screen out particles of inconsistent sizes or any debris, maintaining
the uniformity and purity of the products. Pharmaceutical Industry The pharmaceutical sector demands extremely high precision in material
screening. The linear vibrating sieve machine is used to screen active
pharmaceutical ingredients (APIs) to ensure that their particle sizes are within
the required range. This is essential for the proper formulation of drugs, as
the particle size can affect drug dissolution, bioavailability, and overall
efficacy. For pharmaceutical excipients like starch and lactose, it helps in
obtaining the right particle size distribution for better tablet formation and
capsule filling. Mining Industry In mining operations, the linear vibrating sieve machine is indispensable.
After ores are extracted from mines, it is used to separate the ores based on
their sizes. Coarser ores can be directed to crushing plants for further size
reduction, while the finer ones that meet the required size standards can be
sent for subsequent beneficiation processes like flotation or magnetic
separation. It also helps in removing waste rock fragments and other unwanted
materials from the valuable ores, improving the efficiency of the entire mining
process. Chemical Industry Chemical manufacturing often involves handling numerous raw materials and
intermediate products with specific particle size requirements. The linear
vibrating sieve machine is used to screen chemicals such as fertilizers,
pigments, and catalysts. For instance, in fertilizer production, it ensures that
the different components are mixed at the correct particle sizes for optimal
nutrient release. In the case of catalysts, precise screening helps to maintain
their catalytic activity by providing the right particle size for better contact
with reactants. Recycling Industry In the recycling of materials like plastics, metals, and paper, the linear
vibrating sieve machine is employed to separate different grades or sizes of
recyclables. For example, in plastic recycling, it can distinguish between
different types of plastic pellets based on their sizes, facilitating the
subsequent processing and reuse of these materials. In the recycling of scrap
metal, it helps in sorting out metal pieces of different dimensions, enabling
more efficient recycling operations. Maintenance and Operation Tips Regular Inspection: It is essential to regularly check the condition of the
screen meshes, vibration motors, and the overall structure of the sieve machine.
Any signs of wear and tear, such as holes in the screen meshes or abnormal
vibrations of the motors, should be addressed promptly. Cleaning: Keeping the sieve machine clean is crucial for its optimal
performance. After each use or at regular intervals, remove any residual
materials stuck on the screen meshes and the inner parts of the machine to
prevent clogging and ensure smooth screening operations. Proper Lubrication: The moving parts of the sieve machine, such as the
bearings of the vibration motors, should be properly lubricated according to the
manufacturer's instructions. This helps to reduce friction, extend the service
life of the components, and maintain stable vibration. Correct Installation: Ensure that the sieve machine is installed on a flat
and stable surface, and the inclination angle is set correctly according to the
requirements of the materials to be screened. Incorrect installation can lead to
uneven screening and reduced efficiency. Conclusion The linear vibrating sieve machine is a versatile and efficient tool that
has become an integral part of many industries. Its ability to accurately screen
and separate materials, combined with its advantages in terms of efficiency,
adaptability, and low consumption, makes it a preferred choice for numerous
applications. With proper maintenance and operation, it can continue to
contribute to improving the quality and efficiency of industrial processes for
years to come.
MORE
10
2025-01
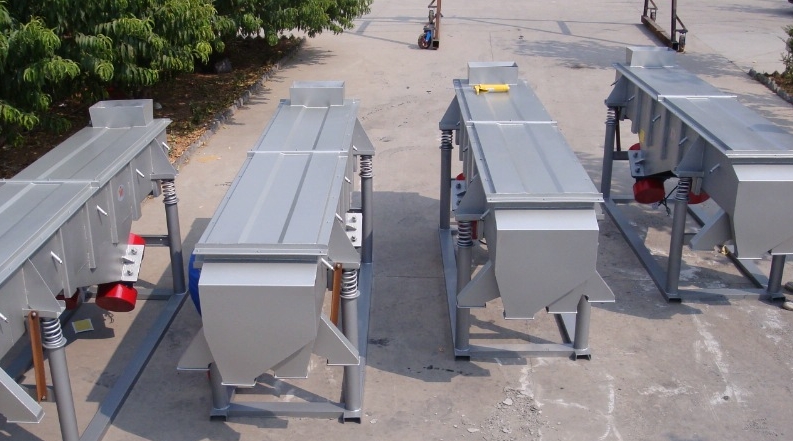
Applications of Rectangular Vibrating Sieve
Rectangular vibrating sieve is a widely used screening equipment in
numerous industries, playing a crucial role in improving production efficiency
and product quality. Here are some of its main applications in different
fields: 1. Mining Industry In the mining sector, the rectangular vibrating sieve is an essential part
of the production process. After ores are extracted from mines, they are in a
mixed state with various sizes and compositions. The rectangular vibrating sieve
can classify the raw ores according to the particle size by setting the
appropriate mesh size of the screen. For instance, larger ore particles can be
separated out and sent for the next crushing process to facilitate the
extraction of valuable minerals later. Meanwhile, the finer ore particles that
meet the specific granularity requirements can directly enter the subsequent
beneficiation processes, such as magnetic separation or flotation. This helps to
enhance the overall efficiency of the beneficiation process and reduce
unnecessary material transfer and energy consumption. Moreover, for different
types of ores like iron ores, copper ores, and gold ores, the rectangular
vibrating sieve can be adjusted with parameters like screen specifications to
precisely meet the screening needs, ensuring the smooth operation of the mining
production chain. 2. Chemical Industry In the chemical industry, strict control over the particle size of
materials is often required in the handling of various raw materials and
intermediate products. The application of the rectangular vibrating sieve is of
great significance. For example, during the production of chemical fertilizers,
it is necessary to screen the powdery and granular raw materials according to
specific particle sizes to ensure that the different components of the raw
materials can be mixed at the appropriate granularity, thus guaranteeing the
stable quality and uniform fertility of the final fertilizer products. When it
comes to the use of catalysts in some chemical synthesis processes, the
rectangular vibrating sieve is also used to screen out catalyst particles within
the required particle size range. Since the particle size of the catalyst
directly affects its catalytic activity and reaction rate, only the precisely
screened catalyst can achieve the best performance in chemical reactions,
improving the efficiency and product quality of chemical production.
Additionally, in the packaging and delivery stage of chemical finished products,
the rectangular vibrating sieve can be utilized to remove impurities or
oversized particles that may have been mixed in, ensuring that the products meet
high-quality factory shipment standards. 3. Food Processing Industry Food safety and quality are of utmost importance, and the rectangular
vibrating sieve makes significant contributions to ensuring food quality. In the
grain processing process, for raw grains such as wheat and rice, before entering
the milling or packaging processes, they need to pass through the rectangular
vibrating sieve to remove impurities like stones, clods of earth, straws, and
shriveled grains that do not meet the requirements. This ensures that the flour,
rice and other products processed later are pure, safe and have good taste. In
the sugar industry, whether it is the raw sugar extracted from sugarcane or the
intermediate sugar products in the beet sugar production process, the
rectangular vibrating sieve is used for screening to grade the sugar lumps
according to size, which is convenient for subsequent refining and packaging
operations. It can also remove the mixed-in fibers and other impurities,
improving the quality of the finished sugar so that consumers can buy sugar
products with fine taste and high purity. For the processing of nuts and candied
fruits, the rectangular vibrating sieve can screen out products with uniform
sizes. On the one hand, it is beneficial for unified packaging and sales, and on
the other hand, it can ensure that the products reach a relatively consistent
standard in appearance and taste, enhancing market competitiveness. 4. Building Materials Industry In the production of building materials, the rectangular vibrating sieve
also holds a prominent position. For example, in the production of sand and
gravel materials, after the stones mined from the quarry are crushed, they need
to be screened by the rectangular vibrating sieve to separate out different
specifications of stones, such as coarse and fine aggregates used for concrete
mixing. Different particle sizes of stones need to be mixed in corresponding
proportions to ensure that the performance indicators such as the strength and
workability of the concrete meet the requirements of construction. In the
production of cement, after the grinding of raw materials and other processes,
the rectangular vibrating sieve is used to screen out the qualified particle
size of cement powder and remove possible large particle agglomerates, ensuring
that the fineness of the cement product meets the standard and thus guaranteeing
the reliable quality of the cement used in construction, making the building
structures more stable. In the ceramic production, after the processing of clay
raw materials, the rectangular vibrating sieve is used to screen out the fine
and uniform parts, which is conducive to the subsequent forming and firing
processes, improving the quality of ceramic products and reducing the defective
rate. 5. Pharmaceutical Industry The pharmaceutical industry has extremely high requirements for the purity
and particle size accuracy of materials, and the rectangular vibrating sieve
also plays a key role here. In the production of active pharmaceutical
ingredients, whether they are extracted from natural medicinal materials or
obtained through chemical synthesis, they need to be precisely screened by the
rectangular vibrating sieve to remove possible unreacted impurities, large
particle agglomerates, etc., ensuring that the particle size of the active
pharmaceutical ingredients is uniform. This enables stable dissolution and
absorption processes in the body when the drugs are formulated into dosage forms
later, meeting the requirements of drug efficacy. For pharmaceutical excipients
such as starch and powdered sugar used as fillers, they also need to be screened
by the rectangular vibrating sieve to obtain products with appropriate particle
sizes. This ensures good forming effects when preparing dosage forms such as
tablets and capsules, and prevents the problem of affecting the drug release and
efficacy due to the particle size of the excipients. In conclusion, the rectangular vibrating sieve, with its efficient
screening ability, good adaptability and stable performance, has become an
indispensable equipment in many industries, continuously promoting the
development and progress of these industries.
MORE
03
2025-01
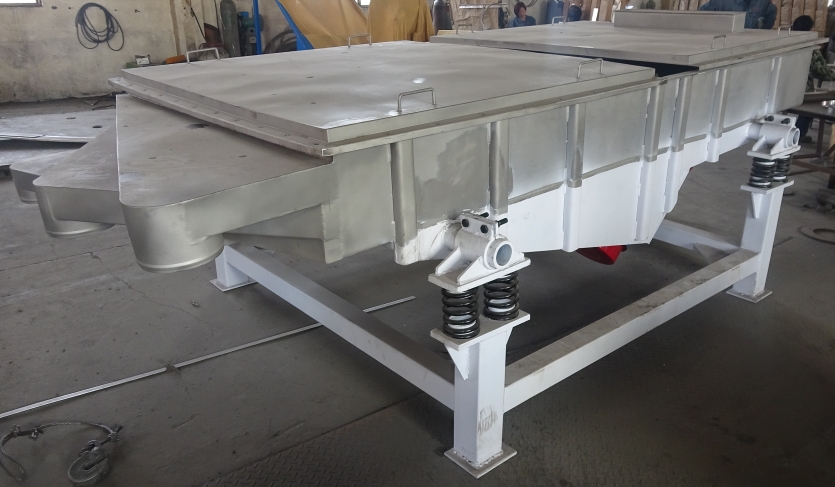
The Practical Application of Rectangular Vibrating Sieve
I. Introduction The rectangular vibrating sieve has become an essential piece of equipment
in numerous industrial sectors due to its outstanding ability to separate and
classify materials accurately. Understanding how to properly use it is crucial
for maximizing its efficiency and ensuring optimal results in various production
processes. II. Installation and Setup Location Selection: Choose a flat and stable surface for installing the
rectangular vibrating sieve. It should be in an area with sufficient space
around it to allow for easy access during operation, maintenance, and material
handling. Avoid installing it in areas prone to excessive vibration from other
machinery, as this could interfere with its normal functioning. Level Adjustment: Use leveling tools such as spirit levels to ensure that
the sieve is perfectly horizontal. An uneven installation can lead to uneven
material distribution on the screening surface and affect the screening accuracy
and efficiency. Make necessary adjustments by adjusting the feet or supports of
the sieve frame until it is properly leveled. Connection to Power and Ancillary Equipment: Connect the sieve to a
suitable power source according to the electrical specifications provided by the
manufacturer. Also, if it is part of a production line, properly connect it with
the upstream feeding equipment and the downstream collection or further
processing equipment. Ensure that all connections are secure and that the
electrical wiring is properly installed and grounded to guarantee safe
operation. III. Parameter Adjustment Vibration Frequency: The vibration frequency determines how quickly the
particles on the screening surface move and jump. For materials with relatively
fine particles and a narrow size range, a higher vibration frequency may be set
to enhance the separation speed. However, for coarser materials or those that
are more fragile, a lower frequency might be more appropriate to prevent damage
to the particles and ensure proper screening. Adjust the frequency using the
control panel or relevant adjustment mechanisms provided on the sieve, usually
in line with the material characteristics and the desired screening outcome. Vibration Amplitude: Amplitude controls the extent of the vibration stroke.
A larger amplitude is beneficial when dealing with materials that tend to
agglomerate or have a high moisture content, as it helps to break up the clumps
and facilitate the passage of particles through the screen mesh. For dry and
free-flowing materials, a moderate amplitude can be selected. The amplitude can
be adjusted through the eccentric devices or other amplitude-adjusting
components on the sieve's vibration system. Screen Mesh Selection: Depending on the target particle size separation,
choose the appropriate screen mesh with the correct aperture size. Finer meshes
are used for separating smaller particles, while coarser meshes are for larger
ones. In some cases, multiple layers of screen meshes with different aperture
sizes can be installed in the rectangular vibrating sieve to achieve a more
refined classification of materials. Replace the screen mesh regularly to
maintain good screening performance, especially when it gets worn or damaged
over time. IV. Operation Process Feeding: Start by evenly feeding the material to be screened into the feed
hopper of the rectangular vibrating sieve. The feeding rate should be controlled
to avoid overloading the sieve, which could lead to poor screening results or
even damage to the equipment. Some modern sieves are equipped with automatic
feeding control systems to ensure a consistent and appropriate material
flow. Monitoring During Operation: Keep an eye on the sieve's operation while it
is running. Check for any abnormal vibrations, noises, or signs of material
blockage on the screening surface. If there are any issues, stop the sieve
immediately and troubleshoot. Also, observe the material flow and the separation
effect at the discharge outlets to ensure that the desired screening results are
being achieved. Discharge and Collection: As the sieve operates, the fine materials that
pass through the screen mesh will be discharged through the corresponding outlet
and can be collected in suitable containers or directed to the next stage of
processing. The oversize materials retained on the screen will move towards the
other discharge outlet and can be removed for further handling, such as
reprocessing or disposal depending on the specific production requirements. V. Maintenance and Troubleshooting Regular Cleaning: After each use or at regular intervals, clean the
screening surface, the interior of the sieve, and the discharge areas to remove
any residual materials. This helps to prevent material buildup, which could
affect the screening performance and also cause corrosion or wear of the
equipment over time. Use appropriate cleaning tools and follow the
manufacturer's cleaning guidelines. Component Inspection: Periodically inspect the vibration motors, bearings,
screen meshes, and other key components. Check for signs of wear, loose
connections, or damage. Replace any worn or damaged parts promptly to maintain
the sieve's stable operation. Lubricate the moving parts as recommended by the
manufacturer to reduce friction and extend their service life. Troubleshooting Common Issues: Uneven Screening: This could be due to an uneven installation, damaged
screen mesh, or improper vibration parameters. Check the level of the sieve,
examine the screen mesh for damage or clogging, and adjust the vibration
frequency and amplitude if necessary. Low Screening Efficiency: Possible causes include incorrect screen mesh
selection, too high or too low feeding rate, or suboptimal vibration settings.
Review these aspects and make appropriate adjustments. Abnormal Noises or Vibrations: It might indicate problems with the
vibration motors, loose components, or foreign objects interfering with the
sieve's operation. Shut down the sieve and conduct a thorough inspection to
identify and resolve the issue. VI. Conclusion Proper use of the rectangular vibrating sieve involves careful
installation, appropriate parameter adjustment, correct operation, and regular
maintenance. By following these steps and being vigilant in monitoring and
troubleshooting, industries can make the most of this valuable equipment to
achieve efficient and accurate material screening and classification, thereby
contributing to the overall quality and productivity of their production
processes.
MORE
03
2025-01
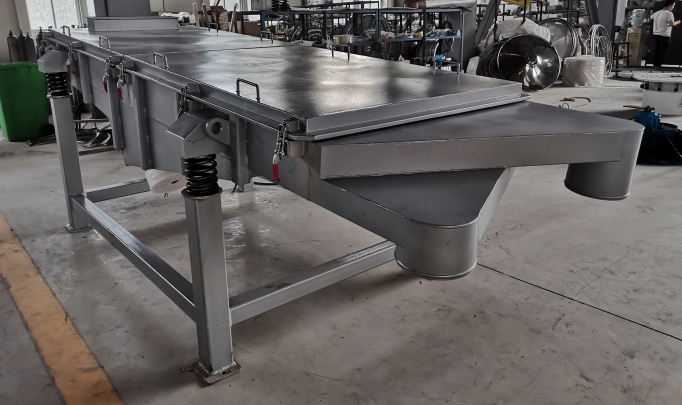
Introduction to Rectangular Vibrating Sifter
I. Overview A rectangular vibrating sifter is a crucial piece of equipment widely used
in various industries. It is designed with a rectangular-shaped screening
surface and operates based on the principle of vibration to separate materials
of different sizes or characteristics. This type of sifter plays a significant
role in processes where precise classification and separation of granular,
powdered, or other particulate substances are required. II. Working Principle The core mechanism behind the rectangular vibrating sifter is vibration.
Motors or other vibration-generating devices are installed on the sifter frame.
They create continuous vibrations that are transmitted to the screening surface.
When the material to be screened is poured onto the sifter, the vibrations cause
the particles to move and jump on the screen. Smaller particles are able to pass
through the apertures of the screen mesh, while larger ones are retained on the
surface and gradually move towards the discharge end for collection. The
frequency and amplitude of the vibrations can usually be adjusted according to
the specific requirements of the screening task, ensuring efficient and accurate
separation. III. Structure and Components Screening Surface: Made of metal wire mesh or perforated metal plates with
different aperture sizes depending on the target separation specifications. The
rectangular shape provides a relatively large screening area, which enhances the
screening efficiency and capacity. Vibration System: Consists of vibration motors, eccentric blocks, or other
vibration-generating elements. The vibration motors are carefully selected and
positioned to ensure uniform and stable vibrations across the entire screening
surface. Frame: Constructed of sturdy materials like steel to support the screening
surface and the vibration system. It is designed to withstand the dynamic forces
generated during operation and maintain the structural integrity of the
sifter. Feed Hopper: Located at the inlet of the sifter, it is used to evenly
distribute the incoming material onto the screening surface, ensuring a
consistent flow and proper screening start. Discharge Outlets: There are usually separate outlets for the screened fine
materials that pass through the screen and the oversize materials that remain on
the screen. This allows for easy collection and further processing of the
different fractions. IV. Advantages High Screening Efficiency: Thanks to the continuous vibration and the
well-designed screening surface, a large amount of material can be screened in a
relatively short time, achieving good separation results for different particle
sizes. Versatility: It can handle a wide variety of materials, including but not
limited to powders in the pharmaceutical industry, grains in the food processing
industry, and minerals in the mining industry. The adjustable vibration
parameters make it adaptable to different material characteristics and screening
requirements. Space-saving Design: The rectangular shape is often more suitable for
installation in industrial production lines compared to some other shapes. It
can be easily integrated into existing setups without occupying excessive floor
space. Easy Maintenance: With its relatively simple structure, components such as
the screening surface and vibration motors are accessible for inspection,
cleaning, and replacement when needed. Regular maintenance can ensure its
long-term stable operation. V. Applications Food Industry: Used for screening flour, sugar, grains, and various food
additives to remove impurities and separate particles of different grades. For
example, in the production of flour, the sifter helps to obtain fine and uniform
flour by removing any lumps or larger particles. Pharmaceutical Industry: Critical for sieving pharmaceutical powders to
ensure the uniformity of particle size, which is essential for drug formulation
and quality control. It helps in removing any foreign particles that could
affect the purity and efficacy of the medications. Mining and Mineral Processing: In the beneficiation of ores, the
rectangular vibrating sifter can separate valuable minerals from gangue based on
particle size differences, facilitating the subsequent concentration and
extraction processes. Chemical Industry: Applied for screening chemical powders, catalysts, and
raw materials to meet specific production requirements regarding particle size
distribution and purity. VI. Conclusion In conclusion, the rectangular vibrating sifter is an indispensable tool in
many industries. Its efficient working principle, reasonable structure, and
numerous advantages make it highly effective for material screening and
separation tasks. As technology continues to advance, we can expect further
improvements in its performance and functionality, enabling it to contribute
even more significantly to the production and quality control processes in
various fields.
MORE
27
2024-12
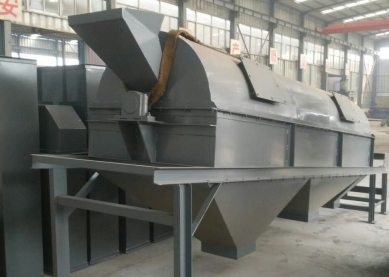
Application of drum screen in domestic waste treatment
The drum screen can be used not only in mining, coke, coal, electric power,
building materials, metallurgy, chemical industry, etc., but also in the
treatment of domestic garbage. For example, after the pretreatment system—sorting and pre-crushing, the
residue of the residue of the kitchen waste, the organic matter of the fiber
plastic cloth, and the recyclable materials such as metal and glass can be
separated by the trommel. After the sludge residue mixture is fermented, the agricultural fine
compost and residual organic matter are separated by a drum sieving machine. The
residual organic matter sieved by the drum enters the nitrogen protection
microwave pyrolysis system together with the fiber plastic cloth organic matter
sorted by the pretreatment system, and the waste can be pyrolyzed to separate
the combustible gas, the liquid residue and the activated carbon. By sorting and processing the wastes step by step to obtain the raw
materials of different components, and carrying out reasonable and advanced
treatment - microwave pyrolysis process, all of them are converted into products
with higher added value, which can improve the resource recycling rate and
improve The purpose of economic efficiency. Therefore, it is suitable for:
national conditions, mature technology, simple process, simple operation, high
resource recycling rate, and complete “resourceization” of garbage; at the same
time, it is completely “harmless”.
MORE
27
2024-12
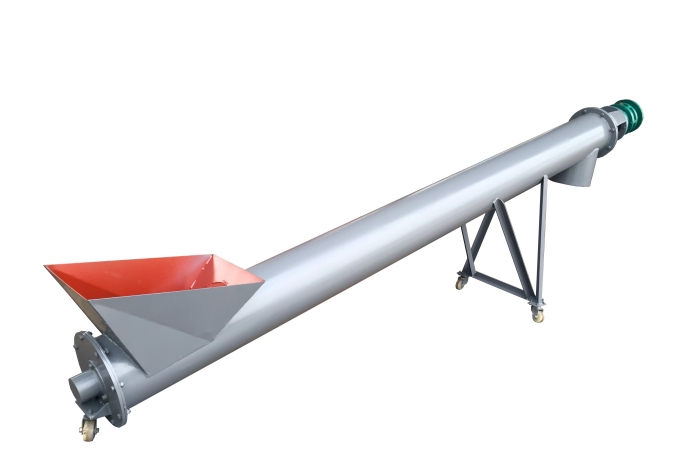
Screw conveyor structure features
1. The screw shaft and the suspension bearing, the head and the tail shaft
are all connected by the tongue type. The installation and disassembly do not
need axial movement, and the maintenance is convenient. , the mandrel is long,
the hanging is less, and the fault point is less; 2, the use of variable diameter structure, increase the volume of the
hanging bearing, to avoid contact between the hanging bearing and the material,
the life of the hanging bearing can reach more than two years; 3. The transmission parts are all connected by floating connection. The
suspension bearing is a universal joint structure, so that the spiral body, the
hanging bearing and the tail assembly form an integral spiral floating body,
which can freely rotate and avoid with the conveying resistance within a certain
range, without jamming. Do not block the material; 4. The head and tail bearing housings are all outside the housing. All
bearings adopt multi-layer sealing and sealing technology, and the bearing has a
long service life.
MORE
20
2024-12
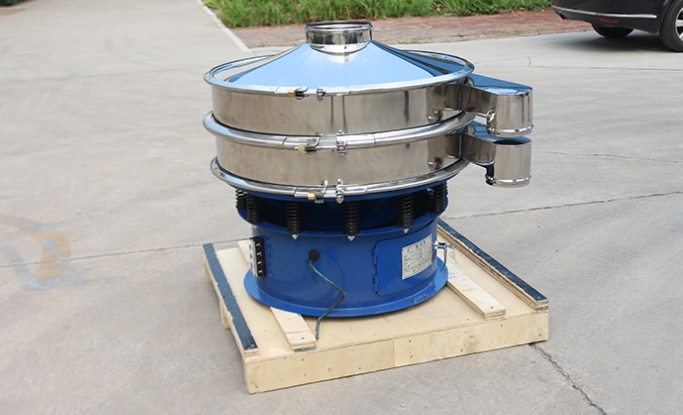
Factors affecting the service life of the vibrating screen
1.Steel Plate of material of vibrating screen: the same material has
different thickness, and different element content will directly affect the
service life of the equipment; The common materials for vibrating screen are Q235 carbon steel and 304
stainless steel. Take the vibrating screen produced by Zhenying Brand vibrating
machinery as an example: Q235 carbon steel sheet thickness is 3.5-4mm for screen
frame, 6mm for bottom barrel, and thickness of 304 stainless steel sheet for
screen frame. 2.5-3mm, bottom barrel 6mm. Secondly, we mainly use fixed and
well-known stainless steel sheet suppliers - TAISTEEL and POSCO. The actual use
environment also affects the service life of the vibrating screen, such as
environmental problems such as moisture and corrosion. 2. Operation of vibrating screen: The nature of the feeding material, the
environment and the feeding method during the use of the vibrating screen will
also affect the service life of the equipment; The nature of the feeding material: such as the shape of the material,
particle size composition, corrosion, static electricity, etc. Production environment: environment such as the humidity of the air and so
on. For example, the location of Southeast Asian customers must be considered in
the selection of raw materials and equipment operations due to the high humidity
of the environment. 3. Design: Design is the foundation of a piece of equipment. Only good
design techniques and knowledge of related industries can design and produce
good quality equipment; In the industry, Zhenying Machinery has entered the vibrating screen
industry since 1999. It has a history of 20 years, including 3 senior engineers
and 1 set of patented production equipment. It has a leading voice in the
industry and equipment related. In addition to the 300 patents, including 10
innovative patents, it is a well-known high-tech enterprise in Henan Province.
At present, an production line with an annual output of 20,000 sets of automated
production line for vibrating screens is under construction. It is expected to
be completed by the end of July this year. 4. Enterprise strength: The hardware and software strength of an enterprise
determines the quality and service life of the equipment produced; The hardware facilities are the primary factors that our company cares
about. In addition to the purchase of general production equipment, automated
crimping and semi-automatic welding equipment is the first manufacturer in the
industry in 2018. In 2019, it cooperates with the famous universities in
Xinxiang City. The automated robotic welding equipment for the screen frame is
now in production. The use of these devices is undoubtedly the revolutionary
significance of industrial optimization in the vibrating screen processing and
manufacturing industry. Software facilities are also another factor in the development of the
company. In addition to a good corporate culture and all people-oriented
corporate development concepts, we are actively introducing management software
suitable for enterprise development to protect the long-term development of the
company. 5. Related accessories: The vibrating screen accessories are made up of
vibration motor, screen mesh, shock absorbing spring, sealing ring and cleaning
net device. The quality of the accessories also affects the life of the
equipment. The service life of a vibrating screen is affected by many factors.
Users should choose a regular manufacturer during the procurement process to
ensure the use of the equipment and subsequent after-sales. In the process of making the vibrating screen, we must ensure the
uniformity and replaceability of each component to ensure the convenience of the
customer to replace the relevant accessories.
MORE
20
2024-12
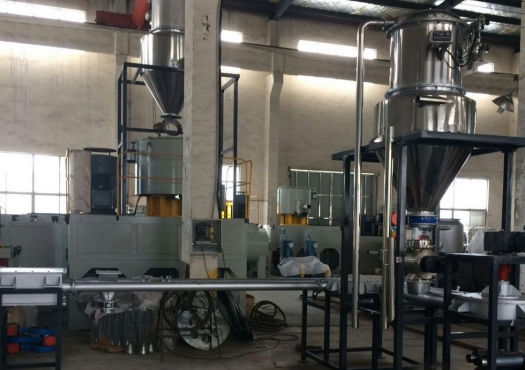
Application of Chain Conveyor in Fertilizer Business
As the “food” of grain, chemical fertilizers play an irreplaceable role in
agricultural production, farmers' income and economic development. The
large-scale use of chemical fertilizers has made China a global fertilizer
producer and consumer. However, the effective utilization rate of chemical
fertilizers and the backward production technology are also the severe situation
that we have to face. Adjusting the structure of raw materials, improving energy
conservation and environmental protection, and achieving production automation
have become effective countermeasures to change the status quo. In the production upgrade of the fertilizer industry, the ton bag unpacking
machine produced by ZHENYING Machinery Co., Ltd. provides equipment support for
the fertilizer industry in terms of energy saving, consumption reduction,
emission reduction and cost-saving. In the process of unpacking the fertilizer,
the ton bag unpacking machine hangs the ton bag into the unpacking machine
through the electric hoist, and then breaks the bag through the artificial
unpacking or cutting knife, then drops the fertilizer raw material into the
rinsing bin, and then passes the conveying. Equipment to the next production
equipment. It is understood that the equipment in the fertilizer production
enterprises, effectively reduce the human participation, reduce the cost of the
enterprise, increase the input speed and production speed, and let the
fertilizer raw materials in the closed environment to carry out bag unloading
operations, avoid dust pollution, improve the workshop working environment. With the increase of national environmental inspections,
environmentally-friendly production equipment has become an essential equipment
for fertilizer plants. TZHENYING Tote Bag Unpacking Machine adopts a closed
chassis design. In addition to its own chemical fertilizer raw materials, it is
not suitable for leakage. It also adds dust collector equipment to collect the
dust generated inside the chassis, and finally falls into the silo below to
successfully solve the dust. Pollution problem, this is one of the reasons why
many fertilizer plants choose this ton bag unpacking machine. In addition, China's aging is intensifying, chemical fertilizer workers are
old, difficult to recruit, artificial and other objective problems, as well as
poor workshop environment, hidden dangers, heavy physical labor and other
practical problems, prompting production automation, unpacking automation,
transportation automation It has become the trend of long-term development of
the fertilizer industry, which also brings opportunities for the ton bag
unpacking machine. Due to the fast unpacking speed of the ton bag unpacking machine and the
remarkable effect of airtight and dust-free, most fertilizer plants have begun
to consult and purchase this new unpacking equipment, and it has been rapidly
popularized nationwide, and the development speed is amazing! The charter also
provides assistance for the transformation and upgrading of the fertilizer
industry, guiding the industry to capacity, complementing the board and
improving quality. The ton bag unpacking machine helps the fertilizer industry
to make a qualitative leap in production scale and product quality!
MORE
13
2024-12
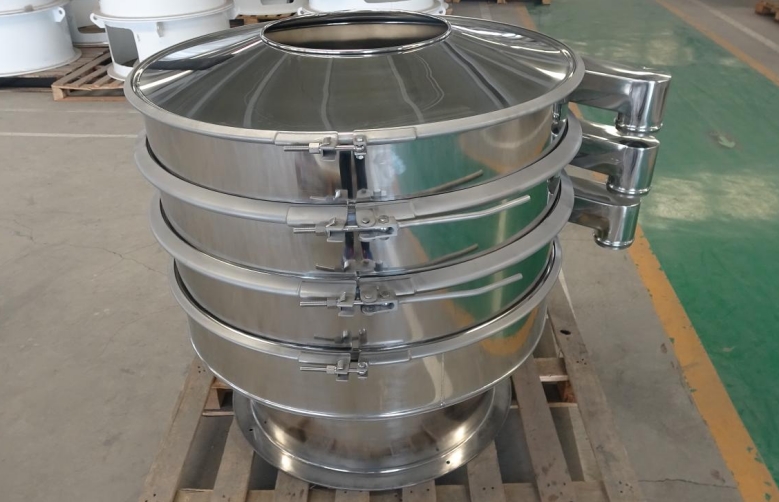
How to choose the suitable vibrating screen
There are many factors to consider when purchasing the vibrating screen.
Some customers may not know more about how to purchase the vibrating screen. In
order to make everyone to purchase a suitable vibrating screen, today we will
introduce some factors that need to be considered when purchasing the vibrating
screen. 1.Your screening purpose.you need fine screening or coarse screening.If it
is fine screening, you need to purchase vibrating screen such as vibrating
screen, ultrasonic vibrating screen, air flow screen, etc. If it is coarse
screening, use linear vibrating screen, mining vibrating screen and straight
screen. 2.According to the properties of the material to be screened. These
properties include: density, shape, temperature, viscosity, particle size,
activity, particle size distribution, and corrosion. 3.The requirements of screening capacity.According to your requirements,
choose the suitable vibrating screen type.our engineer can recommend for
you. 4.Different working environment play a reference role in selecting the
model.
MORE