13
2024-12
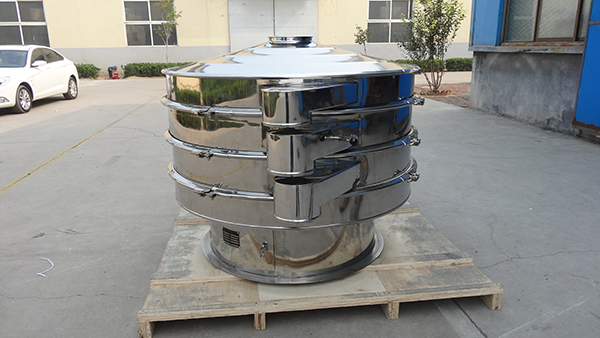
Where does the dangerous source of the vibrating screen come from?
1. Wireline of Vibrating motor :The vibrating motor provides a
corresponding power source for the vibrating screen. If the connecting line is
aging or crushed during use, there will be leakage problems, and if there is
leakage, there will be electric shock or fire hazard. Therefore, in the course
of use, each shift should be checked regularly for the frequency of the line.
Once the damage is found, the line should be replaced immediately. 2. Equipment sealing performance: For some fine powder materials, the
tightness of the vibrating screen is very important. Therefore, when producing
fine powder or flammable and explosive materials, attention should be paid to
the airtightness of the equipment at all times. In case of leakage problems,
stop immediately for maintenance; 3. Operation of large vibrating screen: It is forbidden for personnel to
approach during the operation of large vibrating screen. This is because large
vibrating screen will have a large shaking when working, and damage will occur
once there is a person nearby. Therefore, when the equipment is running, it must
not be opened. After the machine is stopped, wait for the equipment to
completely stop and check it. Please carefully read the relevant instruction manual and operation manual
before using the vibrating screen.
MORE
06
2024-12
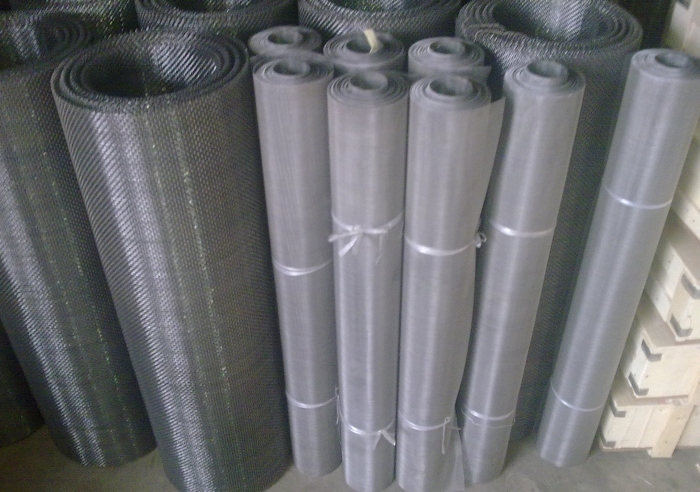
How to prevent the screen of the vibrating screen from being blocked
1. For those materials with more flaky particles, it is necessary to change
the way of the material is broken. 2. For materials with more than 5% moisture in the material, if the
material is dried unconditionally, the sieve surface and the sieve hole should
be selected in a targeted manner to avoid damage to the sieve surface and the
sieve hole. 3. If the material has finer particle size, more mud content, and smaller
sieve size, moisture will play a decisive role in the clogging of the screen, so
we must pay attention to the moisture value of the material during the
process. Reasonable adjustment of the tension of the screen is an effective method
to reduce the plugging of the screen. Reasonable tension force causes the screen
to produce a slight secondary vibration with the support beam, thus effectively
reducing the occurrence of plugging. This can make the screen work better.
MORE
06
2024-12
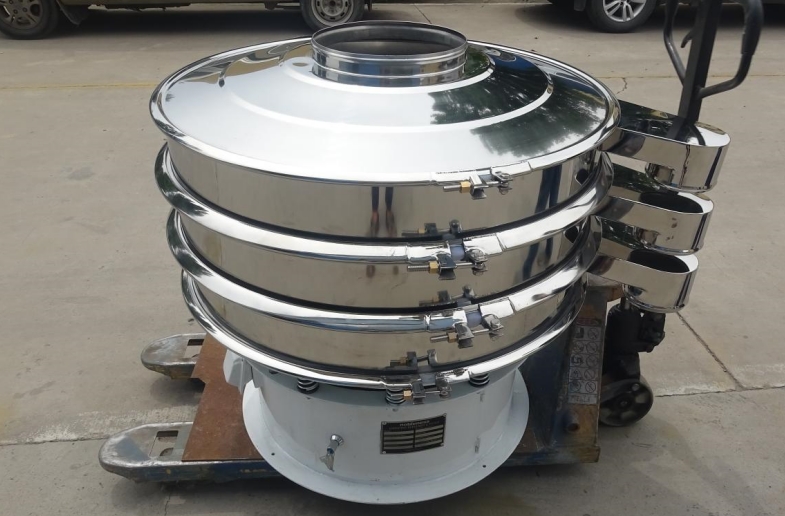
What are the daily maintenance work of the vibrating screen?
1. Maintenance of the vibrating screen; (1) When the vibrating screen is in operation, its vibrating part shall not
be connected or contact with any object outside the machine; (2) When feeding, it should be fed in the width direction of the whole
screen of the feeding port to ensure the uniform distribution of materials on
the screen surface. When the material falls, there shall be no large impact to
avoid damage to the screen; (3) Before opening or stopping, there shall be no material remaining on the
screen surface; (4) If there is abnormal noise during the operation of the equipment, it
should be shut down immediately and checked before being removed. (5) Maintenance of the vibration motor should be checked frequently. 2. Daily maintenance of vibrating screen: (1) Before starting: Check the screen for damage; whether each group of
rings is locked. (2) At start up: pay attention to the presence or absence of abnormal
noise; whether the current is stable; whether the vibration is abnormal. (3) After use: The vibrating screen should be cleaned up immediately after
each use.
MORE
28
2024-11
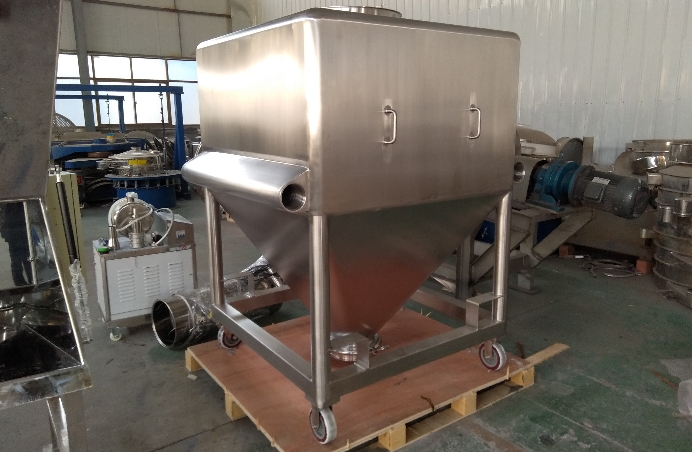
New environmental protection feeding station
With the continuous improvement of China's environmental protection and
ecological safety requirements, as well as the increasingly severe situation of
energy conservation and emission reduction, the environmental awareness of dye
companies is stronger than ever. In the process of my contact with the
enterprise, I clearly realized that in recent years, the awareness of the social
responsibility and the initiative of the company have significantly improved. On
the one hand, the government continues to strengthen environmental governance,
and the environmental violations are becoming more and more strict. On the other
hand, business operators, especially large enterprises, fully realize that
without clean production, enterprises have no room for further development, and
even Will destroy the existing industry. For example, the selection of chemical machinery manufacturing, sand
cleaning, sand mixing, electric welding, grinding, drying of resins and dyes,
packaging, storage and transportation, etc.; here the dye industry has
accelerated the pace of technological transformation of clean production,
continuously improving production around energy conservation and emission
reduction. Equipment, process technology. At this time, Zhenying Machinery
automatic unpacking machine used manual feeding for many production sites, which
not only has low efficiency, but also serious dust on site, seriously
endangering the health of workers, etc., special research and development of new
bag-breaking equipment with independent intellectual property rights, equipment
mainly It consists of seven systems: feeding, bag breaking, screening,
conveying, dust collection, waste bag collection, and automatic control. The automatic unpacking machine overcomes the shortcomings of slow manual
opening and large dust. The structure of the equipment prevents dust pollution,
reduces material and energy consumption, has good sealing performance, avoids
dust leakage, improves working environment, and is safe and explosion-proof.
Moreover, the manufacture of the device can be applied to various sizes of bag
opening and different processing requirements, and the utility model has
multiple uses and saves cost. From the source to prevent occupational disease hazards. For the
construction, technological transformation and technology introduction projects
of new construction, expansion and reconstruction of enterprises, the
construction of a good technical product requires communication with customers,
in-depth understanding of customers, knowing their needs, and developing
products around demand. Define the real problem and then develop the
technology. Zhenying Machinery can realize standardization, large-scale production, or
equipment and equipment. In terms of product quality, product site,
manufacturing, service level, R&D innovation system, solutions, etc., they
all have their own unique features. It is a combination of safety, environmental
protection, energy saving and intelligentization. The products are exported to
more than 60 countries and regions such as the United States, Germany and
Russia.
MORE
28
2024-11
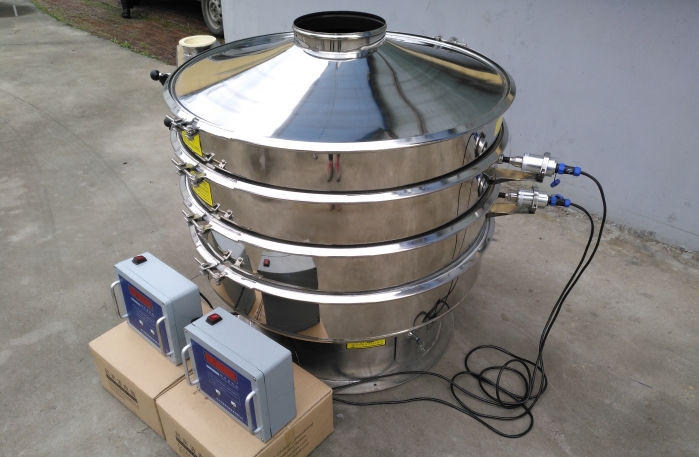
Precautions for ultrasonic vibrating screen during operating
1. The screen or discharge port is at a level: When using an ultrasonic vibrating screen, check that the screen surface or
the discharge port is level. This is directly related to the screening effect of
the ultrasonic vibrating screen; if it is not horizontal, it must be adjusted in
time. The ultrasonic vibrating screen is produced by the support legs, and the
customer can adjust the legs to smooth the ultrasonic vibrating screen and
reduce the vibrating screen accordingly. 2. Adjust the angle of the upper and lower eccentric blocks of the
motor; The angles of the upper eccentric block and the lower eccentric block of
the ultrasonic vibrating screen vibration motor can be adjusted. The smaller the
angle, the faster the material spreads and the angle changes, causing the
material to slowly unfold. When changing the angle of the eccentric block of the
vibration motor, it should be adjusted by about 5 degrees. If the ultrasonic vibrating screen screening accuracy is strictly required,
the motor angle should not be too small, otherwise the material will spread
rapidly, which is not conducive to the screening effect. In the case of an
ultrasonic vibrating screen, the angle of the motor eccentric block is 45°. 3. The height of the screen surface matches the height of the discharge
opening Check that the ultrasonic shaker screen and drain are level or too high.
Under normal conditions, it should be about 5 mm higher. The design of the exit
height of the ultrasonic vibrating screen differs depending on the material
properties.
MORE
28
2024-11
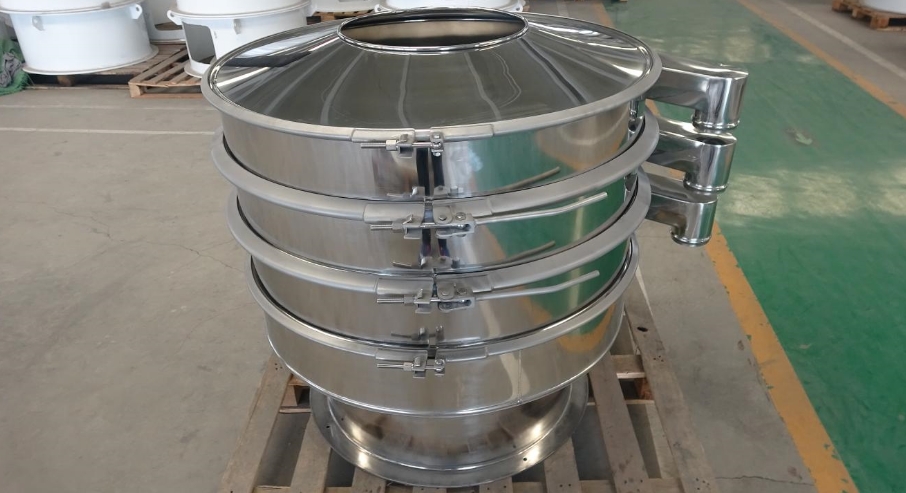
Common fault analysis and problem summary of stainless steel vibrating screen
I: Common fault analysis of stainless steel vibrating screen 1. Due to improper operation; 2. The mesh is blocked; 3. The increase of fine particles and the increase of moisture in the feed
material make the upper layer of the vibrating screen too thick and the feeding
is uneven; Remarks: After the stainless steel vibrating screen has been processed, the
vibrating screen can be reversed for a period of time. The mesh cleaning system
can improve the screening quality of the vibrating screen. II: Summary of common problems in stainless steel vibrating screen: 1. When the stainless steel vibrating screen is in normal operation, the
vibrating screen rotates slowly and the bearing will heat up. When this happens,
the normal maintenance of the stainless steel vibrating screen is not kept up,
resulting in the lack of grease in the vibrating screen bearing. 2. If the stainless steel vibrating screen bearing is a new grease, it may
be the quality problem of the grease or too full, the inferior oil will make the
vibrating screen bearing block the labyrinth seal jam, so the quality of the
vibrating screen grease is very important. . 3. The crack of the side plate of the stainless steel vibrating screen, the
beam is broken, and the structural parts are damaged. This problem is caused by
the working time of the vibrating screen at the critical frequency is too
long.
MORE
28
2024-11
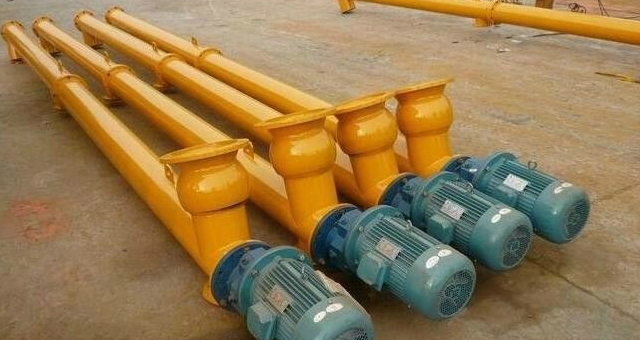
Screw conveyor structure features
1. The screw shaft and the suspension bearing, the head and the tail shaft
are all connected by the tongue type. The installation and disassembly do not
need axial movement, and the maintenance is convenient. , the mandrel is long,
the hanging is less, and the fault point is less; 2, the use of variable diameter structure, increase the volume of the
hanging bearing, to avoid contact between the hanging bearing and the material,
the life of the hanging bearing can reach more than two years; 3. The transmission parts are all connected by floating connection. The
suspension bearing is a universal joint structure, so that the spiral body, the
hanging bearing and the tail assembly form an integral spiral floating body,
which can freely rotate and avoid with the conveying resistance within a certain
range, without jamming. Do not block the material; 4. The head and tail bearing housings are all outside the housing. All
bearings adopt multi-layer sealing and sealing technology, and the bearing has a
long service life.
MORE
28
2024-11
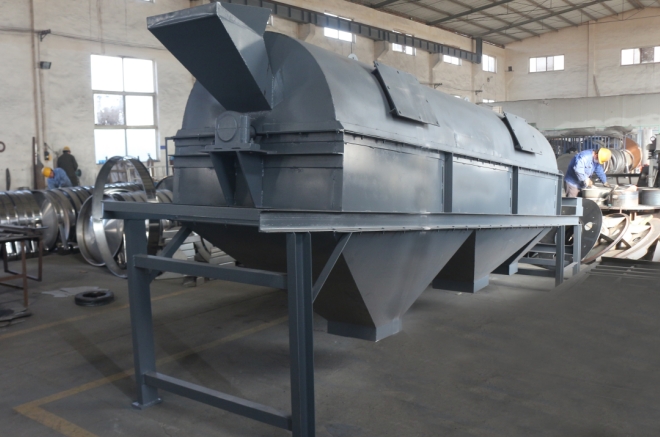
Application of drum screen in domestic waste treatment
The drum screen can be used not only in mining, coke, coal, electric power,
building materials, metallurgy, chemical industry, etc., but also in the
treatment of domestic garbage. For example, after the pretreatment system—sorting and pre-crushing, the
residue of the residue of the kitchen waste, the organic matter of the fiber
plastic cloth, and the recyclable materials such as metal and glass can be
separated by the trommel. After the sludge residue mixture is fermented, the agricultural fine
compost and residual organic matter are separated by a drum sieving machine. The
residual organic matter sieved by the drum enters the nitrogen protection
microwave pyrolysis system together with the fiber plastic cloth organic matter
sorted by the pretreatment system, and the waste can be pyrolyzed to separate
the combustible gas, the liquid residue and the activated carbon. By sorting and processing the wastes step by step to obtain the raw
materials of different components, and carrying out reasonable and advanced
treatment - microwave pyrolysis process, all of them are converted into products
with higher added value, which can improve the resource recycling rate and
improve The purpose of economic efficiency. Therefore, it is suitable for:
national conditions, mature technology, simple process, simple operation, high
resource recycling rate, and complete “resourceization” of garbage; at the same
time, it is completely “harmless”.
MORE
20
2024-11
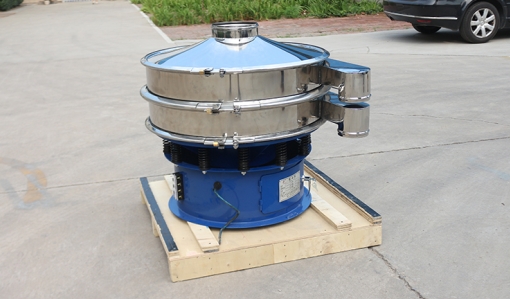
Factors affecting the service life of the vibrating screen
1.Steel Plate of material of vibrating screen: the same material has
different thickness, and different element content will directly affect the
service life of the equipment; The common materials for vibrating screen are Q235 carbon steel and 304
stainless steel. Take the vibrating screen produced by Zhenying Brand vibrating
machinery as an example: Q235 carbon steel sheet thickness is 3.5-4mm for screen
frame, 6mm for bottom barrel, and thickness of 304 stainless steel sheet for
screen frame. 2.5-3mm, bottom barrel 6mm. Secondly, we mainly use fixed and
well-known stainless steel sheet suppliers - TAISTEEL and POSCO. The actual use
environment also affects the service life of the vibrating screen, such as
environmental problems such as moisture and corrosion. 2. Operation of vibrating screen: The nature of the feeding material, the
environment and the feeding method during the use of the vibrating screen will
also affect the service life of the equipment; The nature of the feeding material: such as the shape of the material,
particle size composition, corrosion, static electricity, etc. Production environment: environment such as the humidity of the air and so
on. For example, the location of Southeast Asian customers must be considered in
the selection of raw materials and equipment operations due to the high humidity
of the environment. 3. Design: Design is the foundation of a piece of equipment. Only good
design techniques and knowledge of related industries can design and produce
good quality equipment; In the industry, Zhenying Machinery has entered the vibrating screen
industry since 1999. It has a history of 20 years, including 3 senior engineers
and 1 set of patented production equipment. It has a leading voice in the
industry and equipment related. In addition to the 300 patents, including 10
innovative patents, it is a well-known high-tech enterprise in Henan Province.
At present, an production line with an annual output of 20,000 sets of automated
production line for vibrating screens is under construction. It is expected to
be completed by the end of July this year. 4. Enterprise strength: The hardware and software strength of an enterprise
determines the quality and service life of the equipment produced; The hardware facilities are the primary factors that our company cares
about. In addition to the purchase of general production equipment, automated
crimping and semi-automatic welding equipment is the first manufacturer in the
industry in 2018. In 2019, it cooperates with the famous universities in
Xinxiang City. The automated robotic welding equipment for the screen frame is
now in production. The use of these devices is undoubtedly the revolutionary
significance of industrial optimization in the vibrating screen processing and
manufacturing industry. Software facilities are also another factor in the development of the
company. In addition to a good corporate culture and all people-oriented
corporate development concepts, we are actively introducing management software
suitable for enterprise development to protect the long-term development of the
company. 5. Related accessories: The vibrating screen accessories are made up of
vibration motor, screen mesh, shock absorbing spring, sealing ring and cleaning
net device. The quality of the accessories also affects the life of the
equipment. The service life of a vibrating screen is affected by many factors.
Users should choose a regular manufacturer during the procurement process to
ensure the use of the equipment and subsequent after-sales. In the process of making the vibrating screen, we must ensure the
uniformity and replaceability of each component to ensure the convenience of the
customer to replace the relevant accessories.
MORE
20
2024-11
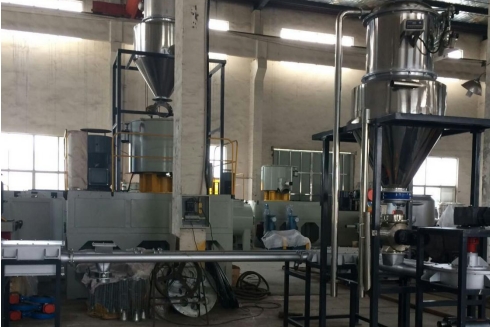
Application of Chain Conveyor in Fertilizer Business
As the “food” of grain, chemical fertilizers play an irreplaceable role in
agricultural production, farmers' income and economic development. The
large-scale use of chemical fertilizers has made China a global fertilizer
producer and consumer. However, the effective utilization rate of chemical
fertilizers and the backward production technology are also the severe situation
that we have to face. Adjusting the structure of raw materials, improving energy
conservation and environmental protection, and achieving production automation
have become effective countermeasures to change the status quo. In the production upgrade of the fertilizer industry, the ton bag unpacking
machine produced by ZHENYING Machinery Co., Ltd. provides equipment support for
the fertilizer industry in terms of energy saving, consumption reduction,
emission reduction and cost-saving. In the process of unpacking the fertilizer,
the ton bag unpacking machine hangs the ton bag into the unpacking machine
through the electric hoist, and then breaks the bag through the artificial
unpacking or cutting knife, then drops the fertilizer raw material into the
rinsing bin, and then passes the conveying. Equipment to the next production
equipment. It is understood that the equipment in the fertilizer production
enterprises, effectively reduce the human participation, reduce the cost of the
enterprise, increase the input speed and production speed, and let the
fertilizer raw materials in the closed environment to carry out bag unloading
operations, avoid dust pollution, improve the workshop working environment. With the increase of national environmental inspections,
environmentally-friendly production equipment has become an essential equipment
for fertilizer plants. TZHENYING Tote Bag Unpacking Machine adopts a closed
chassis design. In addition to its own chemical fertilizer raw materials, it is
not suitable for leakage. It also adds dust collector equipment to collect the
dust generated inside the chassis, and finally falls into the silo below to
successfully solve the dust. Pollution problem, this is one of the reasons why
many fertilizer plants choose this ton bag unpacking machine. In addition, China's aging is intensifying, chemical fertilizer workers are
old, difficult to recruit, artificial and other objective problems, as well as
poor workshop environment, hidden dangers, heavy physical labor and other
practical problems, prompting production automation, unpacking automation,
transportation automation It has become the trend of long-term development of
the fertilizer industry, which also brings opportunities for the ton bag
unpacking machine. Due to the fast unpacking speed of the ton bag unpacking machine and the
remarkable effect of airtight and dust-free, most fertilizer plants have begun
to consult and purchase this new unpacking equipment, and it has been rapidly
popularized nationwide, and the development speed is amazing! The charter also
provides assistance for the transformation and upgrading of the fertilizer
industry, guiding the industry to capacity, complementing the board and
improving quality. The ton bag unpacking machine helps the fertilizer industry
to make a qualitative leap in production scale and product quality!
MORE